New dry section for Pfanner
Pfanner, a loyal and long-standing customer of Profipack, was planning to build a new dry section in a production facility in Vorarlberg and commissioned Profipack to do so. After several layout optimisations, a system solution was found in consultation with the local contacts that offered the necessary flexibility in terms of output and product range to allow for future developments.
The new line enables the customer to process eleven different products. Despite the large number of formats and product types, it was possible to design a system solution with an extremely short changeover time of just 15 minutes. Bottles of 0.2 litre, 0.25 litre, 0.33 litre, 0.35 litre, 0.5 litre and 1 litre are handled. These can be packaged at an output of 28,800 bph.
As a supplier of complete system solutions, Profipack also took on the project planning and hardware and software integration of external systems (crate washers, etc.). Thanks to good project management and many years of experience, the line was successfully put into production after an installation time of 21 days. The following machine technology was used in Profipack's turnkey solution for this project:
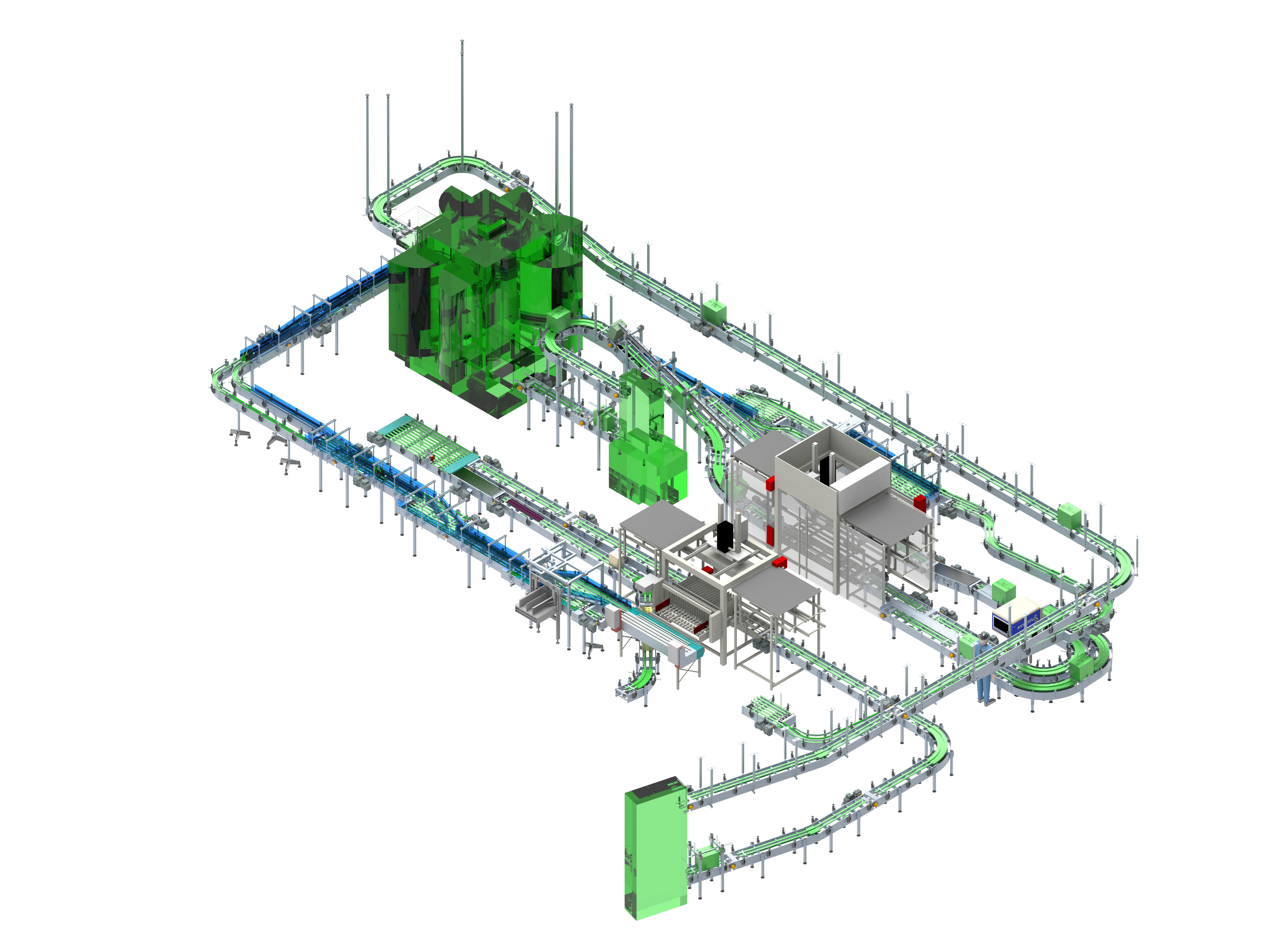
Detail of the system supplied
Packer
The packer consists of the basic machine: 2-axis gantry packer with a table width of 1200mm. In order to be able to process the large number of bottle formats, the packer was equipped with three format parts, which are stored in a quick-change magazine. The customer already had two further sets. These were converted to fit the PROFIPAC.
The bottles are lifted from a bottle table and placed in the allocated plastic crates. The packer can fill up to three crates with one stroke. It therefore achieves an output of 28,800 bottles per hour.
Transporters
In total, approximately 83 metres of bottle conveyors and 55 metres of container conveyors have been installed throughout the dry section. The conveyors are made of stainless steel and equipped with stainless steel hinged belt chains and accumulation roller chains. Tight curve radii have enabled the compact design to be achieved.
The bottle conveyors are also fitted with stainless steel slat-band chains. The system is designed with belt lubrication to ensure smooth and gentle bottle transport.
Unpacker
Similar to the packer, the unpacker consists of the same basic machine. However, the unpacker has a hold-down device for the crates. Here too, there are five different format sets, two of which are already provided by the customer and only need to be slightly modified.
The format parts can be easily changed manually via an ejection station.
In order to achieve the highest possible output, there is a control system in front of the unpacker that checks the unpackability of the crates. If this is not the case, the crate is sorted out manually.
Crate washer
For the crate washer, Profipack turned to a well-known supplier with a reputation for high quality and good performance. They supplied a spiral washer for cleaning the unpacked crates. This washer is equipped with self-cleaning, a heating register, monitoring of the crates and automatic dirt removal. The supplier also supplied a C chute. This allows the crates to slide down and turn around during the sliding phase, so that the crates can be washed upside down.
About the client
Hermann Pfanner Getränke GmbH
For over 160 years, the family-owned company Hermann Pfanner Getränke GmbH has been inspiring people with its philosophy of doing its best to produce high-quality products from the gifts of nature. In the same way, fruit juice has been inspiring people for a long time with its taste, enjoyment and refreshment. It all began when Max Hermann Pfanner bought the "Gasthaus Hirschen" in Lauterach with its small brewery and distillery. Even then, schnapps was distilled from local fruit, especially apples and pears. Back then, no one could have imagined that the company would grow into one of the largest apple processors in Europe. Pfanner is 100% family-owned by the Pfanner, Schneider and Dietrich families, who run the company together with external management.
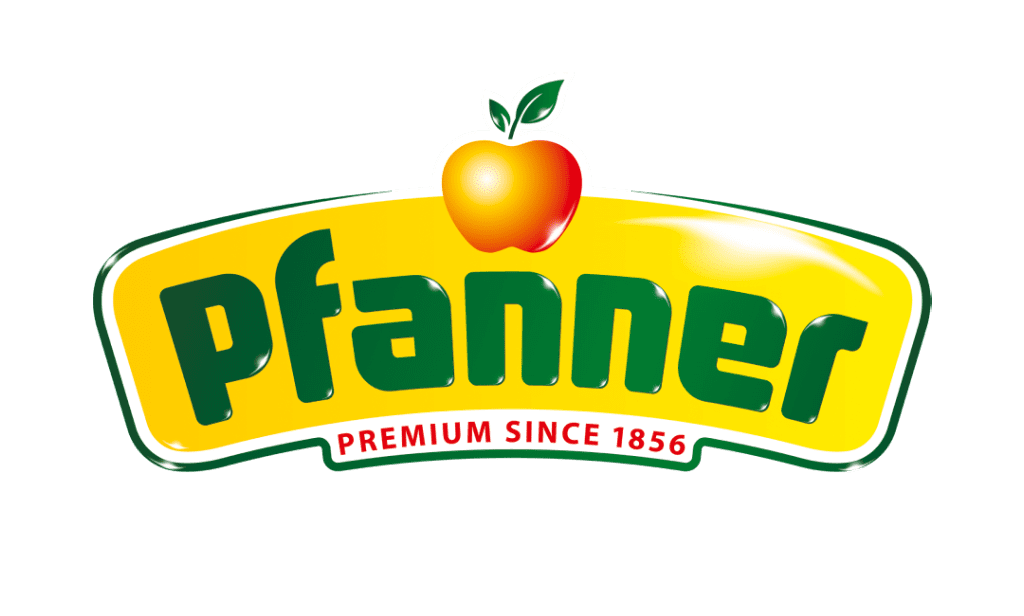